The field of green materials has become a new "battleground" of competition.
In recent years, vehicle indoor air quality has become one of the important criteria for consumers' purchase, with the impact of foreign environmental protection concepts and the upgrading of the demand structure of domestic consumers. According to the investigation report of the automobile industry, the number of consumer complaints about the vehicle interior odor grew year by year, which increased by more than 23 times from 2014 to 2019 with the complaint rate mounting by 16 times.
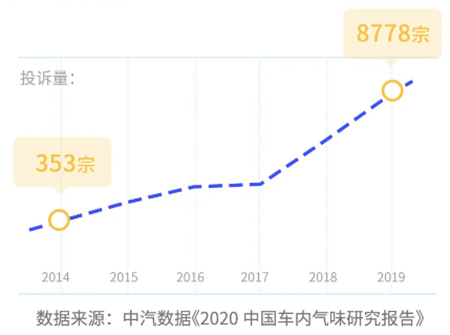
Data source: 2020 China Vehicle Interior Odor Research Report published by CATARC
Blunt comments such as "It smells bad in the car." and "There is a strong smell of rubber inside the car." have a significant impact on consumers' choice. The higher the vehicle interior odor level is, the faster the consumer's recommendation to the car decreases.
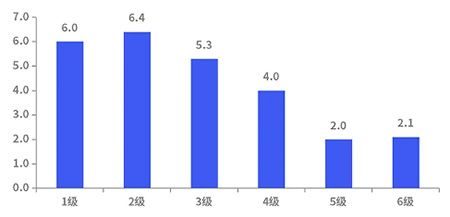
Data source: 2020 China Vehicle Interior Odor Research Report published by CATARC
Vehicle interior odor mainly comes from the materials used in seats, sound insulation cotton, air conditioners, carpets and other parts. Therefore, in order to improve the vehicle indoor air quality to respond to consumers' demands for environmental protection and health, automakers entail controlling the quality of green materials, so that they may gain an advantage in the next stage of market competition.
Current challenges of the automobile industry chain to manage and control green materials
However, in fact, automakers often confront challenges and risks in the strict management and control of automotive green materials. There are tens of thousands of components in a car, and each product has different testing standards and experimental requirements because of its specific materials, designs, functions and so on. Therefore, if automakers want to verify and supervise all the products of all parts, they will be given an immensely heavy workload.
Chances are that automakers have to locate the source and find the reason in dozens or even hundreds of components if they find that the test results of the overall VOC and odor in the car are not up to standard only after the development, production and assembly of all the components. The whole process is as complex as Sherlock Holmes investigation, which may not only delay the project, but also bring high rectification costs to the enterprise, affecting its benefits. Therefore, it has become a consensus of more and more automakers to control the selection of materials from the source to develop environmentally friendly cars.
GRGTEST: Help automakers to choose green materials from the source
GRGTEST can provide VOC, harmful substance and odor control for raw materials, components and vehicle industry chain. At the same time, it also has rich experience in odor rectification to trace the source of vehicle indoor air quality problems and provide mature rectification programs for manufacturers. That is how GRGTEST help the automobile industry chain to manage and control green materials from the source, and solve the problems encountered in product management and control.
Dong Jia, an expert of automotive chemical technology in GRGTEST, said that GRGTEST, as a third-party measurement and testing organization, can make use of integrated advantages to help automakers reduce costs and improve efficiency. GRGTEST, especially aiming at the problems of the automobile industry chain, extends the technical service to the design and selection of materials, and helps automakers to improve their ability to choose green materials through material composition analysis technology. GRGTEST can provide a series of services, such as helping automakers to establish management and control standards, verification and risk assessment of suppliers' materials, customized foreign material analysis, polymer composition analysis.
① Vehicle interior odor traceability and rectification services
Results:
1. To help automakers reduce vehicle interior odor
2. To establish a database of key odor substances gradually
3. To realize the quantitative control of odor level, rather than subjective evaluation
4. To make a high-risk control list to reduce the cost of management and control
② Control of consistent VOC content in production
Identify the target substance, formulate the control list, and carry out rectification and verification through the delamination traceability of the whole vehicle (whole vehicle/components/materials). The top 25 largest volatile organic compounds and aldehydes and ketones except the 8 controlled substances are analyzed to assist enterprises to understand the control requirements of volatile organic compounds in advance that may increase in the future and reduce the control pressure in the future.
Advantage I: To improve testing efficiency and reduce costs
Previous management and control modes of VOC and odor: During the project development phase, the overall VOC and odor in the vehicle is measured only when all components are developed, produced, assembled and the project is nearing completion. If the overall test results are not up to standard, the VOC and odor in each component and material will be tested then. This mode that the product is found to be unqualified in the final stage of the project development without any VOC data support of components and materials will lead to investigation lag and no reasonable rectification direction, affecting the project cycle and even the whole vehicle production cycle.
Advantage II: To obtain the real data to control the quality of the components at the source
Direct cooperation between automakers and GRGTEST can avoid the situation that the samples have been processed by downstream suppliers and that actual samples are not consistent with the reported results, ensuring automakers understand the true environmental protection level of materials or components.
Advantage III: To unify test standards to make production cycle data traceable
Only one model's VOC and odor are tested in a laboratory to ensure the consistency of the implementation standards and testing process, making the data continuous and complete. In this way, it is easy to trace the data of materials and components.
Advantage IV: To accumulate data to provide accurate guidance
With the continuous accumulation of material and component data of a vehicle model, we can find out the reasons for the unqualified products simply and quickly, and put forward the direction of rectification and improvement.
Help automakers to improve the quality of green materials with failure analysis technology
Failure analysis is a new developing discipline, which has been widely used in the fields of material precipitate analysis and performance defect analysis in recent years. GRGTEST creatively applies this technology to improve the quality of green materials to find the key raw materials of products and carry out rectification and improvement, in order to establish a green material database for automakers.
For example, automotive EPDM/EVA materials have no odor at first, but they will produce odor after being used for a long time. We can trace the source to find the odor substances, analyze its composition and determine the specific components that produce the odor. Next, we will simulate temperature, humidity, light and other conditions to find out the mechanism of odor. Finally, we will update the standards to prevent similar cases in the future.